
Thankful to ISRO to have supported us with our subscale engine tests that gave us the confidence to go ahead with larger engines of the same type. This engine was completely manufactured at Agnikul's Rocket Factory - 1. I am grateful and lucky to be blessed with an incredibly hardworking team that pulled off end-to-end engine design, manufacturing & testing in-house. A continuous 108 second burn was also a wait like no other! Arnold witnessed the first flight test of the British turbojet designed by Frank Whittle. In May 1941, as construction of the AERL was just beginning, U.S. Working with subcooled LOX was an experience like no other. Emergence of the Jet Engine Unbeknownst to the NACA, however, both German and British engineers in the 1930s were designing a new more powerful aircraft enginethe turbojet. Thankful to the IN-SPACe team to have come in person & experienced this live with all of us. Humbled to announce the successful completion of the flight acceptance test of our 6kN Agnilet engine that will be used for our upcoming controlled suborbital flight. #deeptech #berlinstartup #space #henryfordmoment Then you will be faced with NRE even if you have a design that could potentially do it without. You certainly can optimize the satellite in that way but later on it will restrict new payloads and missions. If a certain version of your bus does not have all elements, then there is the temptation to place other elements (bus or payload) in those places that are currently unoccupied. no star tracker for a 100% nadir mission) is usually not worth it, just fly it anyway.ģ) mechanically incompatible bus configurations Also reducing a working avionics by one subsystem just because a mission has lower specification (e.g. If it cannot be avoided then push all changes of a system towards one point of the satellite (for example a payload management system) rather than changing all bus systems a little. Then you need to review and requalify all affected systems. Opening up an electrical design and to produce a modification might see easy but there are many more things to do, new connectors, new harness, thermal and data problem. Except for deep space extra launch mass is almost certainly always cheaper than engineers.įor all the love we have for optimizing bus subsystems, don't do it. So best avoid that and just add dedicated balance masses.
#Nasa picture of the day jet engine test software#
Yes, there is software that helps you to automate parts of this work but you will be surprised how, person hours stack to person month and years easily as soon as you have a few people involved. Even small changes can eat up years of engineering work. It looks attractive because you save mass but in the end you have to touch the mechanical design of the satellite and have to redo the harness routing and then need review all of it.
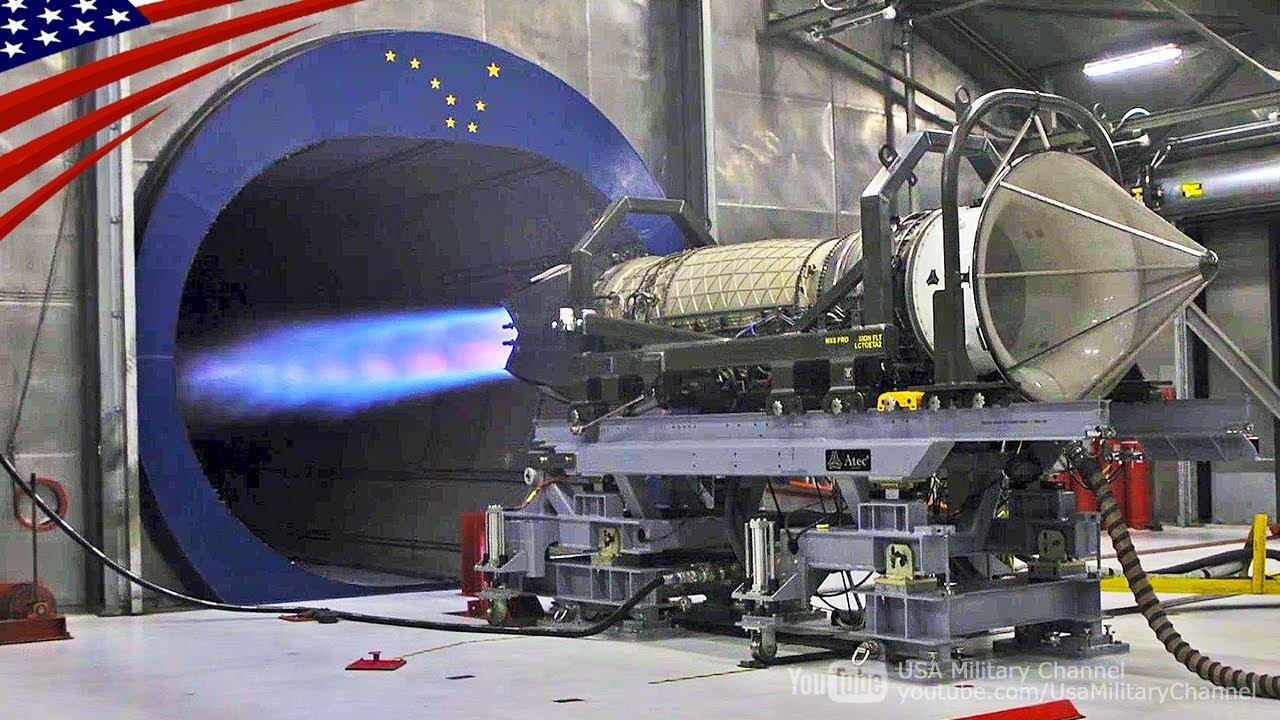
Here are three common mistakes and why to avoid them.ġ) moving bus subsystems to balance MoI of the payload: To save cost in space missions: be religious about low NRE.
